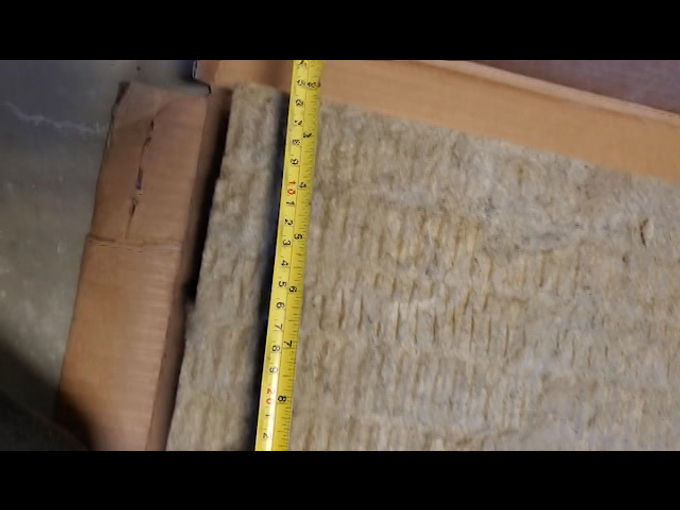
Contruction
This project was conceived, analyzed, and designed at CWU. Working with the constraints of the university resources and the budget of the JCATI project, parts will be bought from different distributors and assembled using university resources. These bought parts will be made of a 20-gauge steel sheet for the enclosure, a 2 in mineral wool for insulation, and a heat-resistant vinyl sheet to cover the conveyor hole. To assemble and manufacture the parts it will undergo a decision matrix to show what the best option will be.
Figure 2 shows a matrix for deciding how holes/steel sheets will be cut. The options included power tools, laser cutter, and CNC (plasma cutting). The main criteria are based on was its availability, knowledge of the equipment, and the accuracy of the device. With those factors in mind, they were weighted at different in order of risk. Knowledge of the equipment leads to the most risk, so it was weighted 3 times the usual. Availability is the next one with the most possible risk, so it was weighted 2 times the usual. Finally, the accuracy was also weighed 2 times the usual since not having accurate cutes can lead to misalignments in assembly which is a potential risk. Thus, the matrix showed that using a CNC was to be the best option and the laser cutter and power tools fell shortly after.
Appendix F-2 shows a matrix for deciding how to assemble the encloser together. The options included welding, power tools, and welding paste. Welding showed high points on accuracy, availability, and efficiency. What made this a less viable option compared to power tools is the knowledge of using the equipment since the project engineer has not taken the welding class at the university and is not verified to use the equipment. Even with this lack of knowledge welding showed to be the best assembly process over power tools and welding paste.
From Appendix F-3 and Analysis 1, a material selection- 2-inch mineral wool was selected on the requirement of keeping 500C inside and 45C surface temperature. From the matrix, it showed that the major factors that it was chosen were its heat resistance and the high R-value that it had. These two components were crucial to the analysis and are the main reason it became the number one contender for material selection. These two components were also weighted the most in the matrix because of their importance to the analysis and if either of the components then it would not be a suitable material for the application. The other component of the matrix was the thickness, the mineral wool was 2 in thick which was not the most suitable compared to the thermal blanket that was 1 inch thick. This component was weighted on a scale of one since the thickness was not a crucial part of the analysis and was only considered to keep the enclosure smaller and easier to handle. Since this component was not weighted as heavily it made mineral wool the best material to select compared to the thermal blanket and the polyisocyanurate insulation.

Figure 2: Matrix 1 cutting decision

Figure 3: Matrix 2 assembly decision
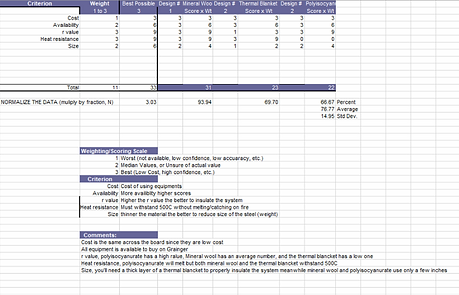
Figure 4: Matrix 3 material decision for insulation